Invited Speakers
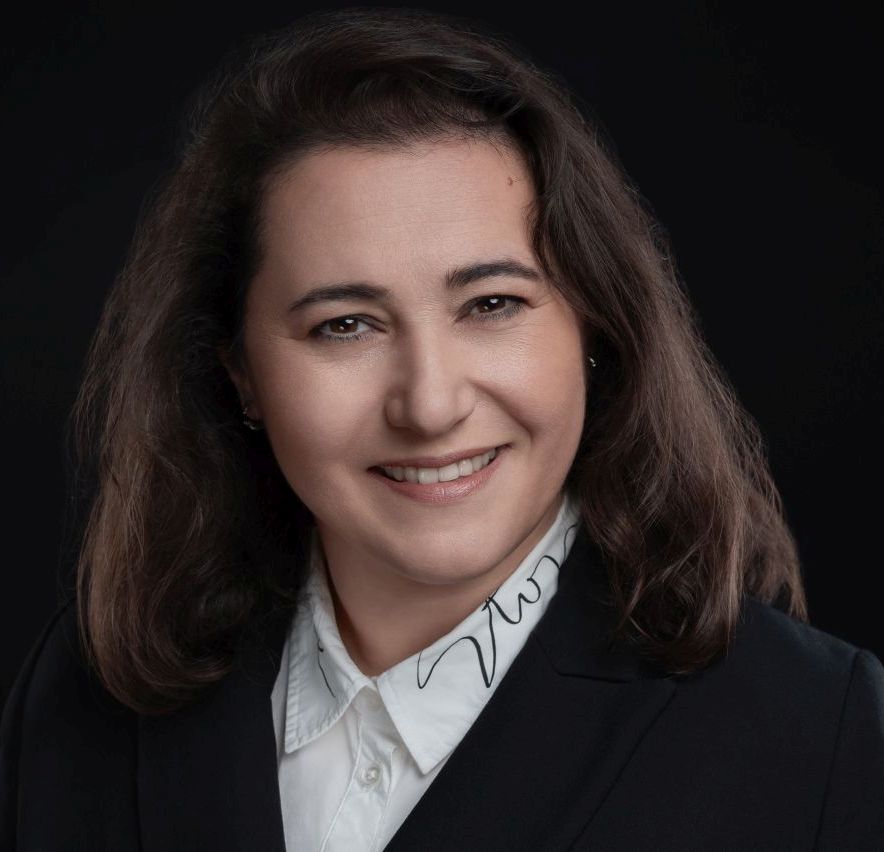 |
Keynote Speaker
Urszula Stachewicz is a professor of materials science at AGH University of Krakow, Poland, where she leads the Electrospun Fibers Group. She earned her PhD from Delft University of Technology in the Netherlands, specializing in the electrohydrodynamics of liquids, with research conducted at Philips Research Laboratories in Eindhoven. Following her PhD, she pursued postdoctoral research at Queen Mary University of London, UK, and worked at the spin-out company Nanoforce Technology Ltd., focusing on polymer science and electrospun fibers. In 2018, she was a Visiting Fellow at the University of Cambridge in the Department of Materials Science and Metallurgy, where she expanded her expertise in piezo- and triboelectric materials. Her research centers on the surface and bulk properties of electrospun fibers for applications in biomedicine, water and energy harvesting, as well as in situ mechanical testing of synthetic and naturally structured materials. She has also pioneered advanced 3D tomography protocols using focused ion beam and scanning electron microscopy (FIB-SEM) for studying nanofibrous biomaterials and membranes. In 2020, Prof. Stachewicz was awarded a prestigious ERC Starting Grant for her groundbreaking research. More details about her work can be found at fibers.agh.edu.pl. |
Structure-properties relationship in electrospun polymer and composite fibers
Urszula Stachewicz
Electrospinning enables the production of polymer fibers with unique properties by applying an electric field between a nozzle fed with the polymer solution and a counter-electrode. As the jet forms and the solvent evaporates, solid fibers are produced. The electric field not only aligns polymer chains to create supramolecular structures with enhanced mechanical or piezoelectric properties but also reorients functional polymer groups, modifying surface chemistry and potential. Furthermore, nanoparticles or other fillers can be incorporated into the polymer solution to produce composite fibers with synergistic properties, such as improved mechanical resilience or enhanced electrical and thermal conductivity. Advanced characterization techniques, including atomic force microscopy (AFM), Kelvin probe force microscopy (KPFM), piezoresponse force microscopy (PFM), and in situ tensile testing, allow for precise analysis of the structure-property relationships in both individual fibers and fiber meshes. These insights enable the design of fibers with tailored properties for diverse applications, including tissue engineering, drug delivery, and water and energy harvesting. |
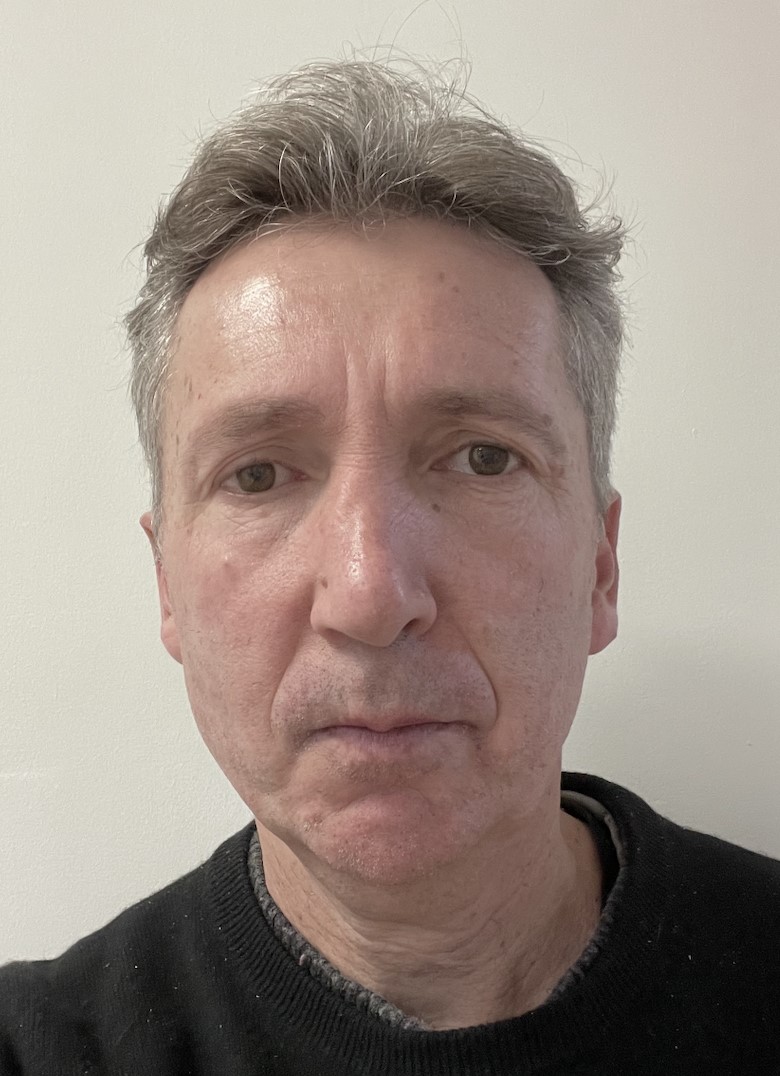 |
Marc Legros, born on March 16, 1967, in Marseille, is a distinguished Directeur de Recherche (DR1) at CNRS and a leading scientist at CEMES-CNRS in Toulouse, France. He earned his Ph.D. from Paul Sabatier University in 1994 and conducted postdoctoral research at Johns Hopkins University. Marc has held notable positions, including a CNRS researcher role in Nancy before his appointment in Toulouse. He has received prestigious awards, such as the CNRS Silver Medal, the Constellium Prize from the French Academy of Sciences, and the Bessel Prize from the Humboldt Foundation. His research, encompassing crystalline defect analysis, advanced materials deformation, and machine learning applications in TEM, has resulted in over 120 publications. Passionate about science and family, Marc lives with his wife, Marie-Pierre, their four children, and a collection of pets and "classic" French car. |
In situ TEM straining: old tricks and new artefacts. An intrinsically small-scale testing method
Marc Legros1, Frédéric Mompiou1, Stephan Sandfeld2, and Daniel Caillard1
1 CEMES-CNRS, 31055 Toulouse, France
2 Forschungszentrum Jülich, 52425, Jülich, Germany
The mechanical properties of metals and alloys are dictated by the individual and collective behavior of dislocations but very few techniques allow to observe them dynamically. In situ TEM straining is among those, and surprisingly, its use has remained rather confidential over the last 6 or 7 decades. The recent advent of in situ TEM nanoindentation holders in conjunction with the renewed interest in micro-and nanoscale plasticity have shed light on the possibilities of this technique, sometimes at expenses of the legitimate doubts cast on the artifacts linked to in situ methods (sample size, image forces, electron beam interaction…) Being able to measure a force and a deformation on tiny or complex-shaped samples has also become a stand-alone goal of such in situ studies, often missing the real opportunities that represent a detailed analysis of the dislocation behavior. Here, we will show that such analysis, either using classical elasticity theory or by taking advantage of more recent machine learning can lead to significant advances either in high entropy alloys, pure metals, and revive some old-fashioned metallurgy in small volumes. |
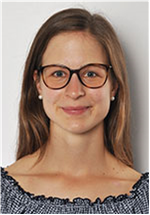 |
Martina Freund is a Postdoctoral Researcher at the Institute for Physical Metallurgy and Materials Physics, RWTH Aachen University. Her research focuses on the plasticity of complex intermetallic phases, continuing the work from her PhD. She aims to elucidate dislocation motion in Laves phase structures and extend these findings to approximately 1,400 known phases. Her approach integrates advanced characterization techniques, including SE, EDS, EBSD, and TEM, alongside nanomechanical deformation methods such as indentation and micropillar compression. By examining the effects of temperature and chemical composition, her work contributes to a deeper understanding of dislocation mechanisms in these materials. |
Plasticity of Ca-Mg-Al C14 and C15 Laves Phases and its Temperature and Chemistry Dependency
Martina Freund, Zhuocheng Xie, Pei-Lin Sun, and Sandra Korte-Kerzel
Institut für Metallkunde und Materialphysik, RWTH Aachen University
Understanding dislocation motion is essential for predicting materials behaviour and being able to manipulate properties. For standard crystal structures there is plenty of literature on how dislocations move through the lattice and how they can be influenced. For more complex phases there are little known, limited by the fact of its inherent resistance against dislocation motion at ambient temperature due to the topologically closed packed structure. This leads to a huge gap of knowledge regarding the dislocation behaviour below the brittle ductile transition temperature. One of the most common intermetallic phases are the Laves phase coming up to more than 1400 different compounds, for all three prototypes. The fact that these are built with similar building blocks, just slightly rearranged, suggests that the dislocation behaviour is transferable within its prototype, but also between the different prototypes. We aim to understand the key fundamental principle of the dislocation behaviour of the forming hexagonal C14 CaMg2 and cubic C15 CaAl2 Laves phases and how this is affected by changes in chemistry and deformation temperature. With nanomechanical methods such as nanoindentation and micropillar compression testing, plasticity can be introduced locally and analysed quantitatively by evaluating the resulting slip planes and their activation frequency, and qualitatively by determining the critical resolved shear stress of specific systems. In addition, transmission electron microscopy helps to unravel the plasticity beneath the indentation by determining the dislocation Burgers vectors and confirming the slip planes. A deeper understanding of the dislocation behaviour is gained by varying the influencing factors such as chemistry and deformation temperature. Mechanical properties, such as hardness and indentation modulus, are found to remain constant for the hexagonal C14 Laves phase in its studied range up to 250°C, but dislocation motion appears to be facilitated by temperature, as indicated by the decrease in the number of serrations with increasing temperature. On the other hand, the change in chemistry, and therefore the deviation from the stoichiometric composition, results in a decrease in hardness and indentation modulus for both Laves phases. In contrast to the macroscopic test above the BDTT the majority of the observed dislocation motion is on the non-basal planes. Especially for the cubic C15 Laves phase additional planes, the {11n}, are found to be the favoured planes for dislocation slip, which seems to facilitate their motion additionally by cross-slipping from one {11n} to another {11n}. Atomistic simulations explaining these motion by calculation the minimum energy paths for these planes. The analysis of the resulting plasticity at room temperature and that due to changes in deformation temperature and chemistry will lead us to a better understanding of the fundamental principle of dislocation motion in these complex phases. Initial results have provided new insights into possible slip systems, dislocation motion and mechanical properties. |
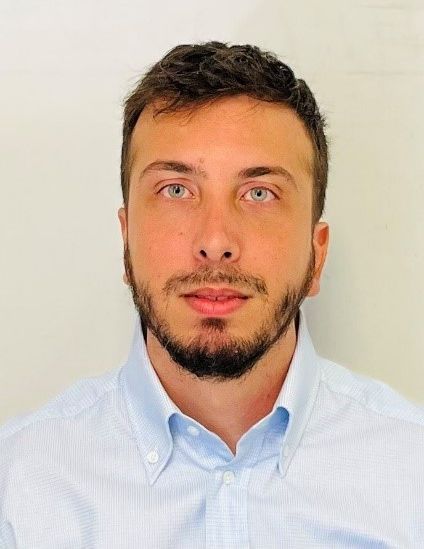 |
Edoardo Rossi specializes in high-speed nanoindentation mapping, the fracture mechanics of 3D-printed nano-ceramics, and the application of machine learning to materials characterization. He is currently an Assistant Professor at Università degli Studi Roma Tre. Since 2022, he has served as Assistant Managing Editor for Materials & Design and has co-led Virtual Special Issues on AI in Materials Science and Nanomechanical Testing. Additionally, he is one of the co-leaders of MecaNano WG4, focusing on Machine Learning in nanomechanics. |
Decoding Microstructures: Machine Learning for High-Speed Nanoindentation Mapping
Edoardo Rossi
High-speed nanoindentation mapping generates vast datasets that capture mechanical property variations across complex microstructures. However, effectively interpreting these large-scale maps requires advanced data-driven approaches. This talk explores how machine learning techniques, including clustering and deep learning, can be leveraged to deconvolute mechanical maps, revealing distinct micro-constituents, phases, and structural features. By integrating nanoindentation data with complementary characterization methods, such as EBSD and EDX, we uncover hidden correlations between mechanical properties and material heterogeneity. Machine learning accelerates phase identification and trend extraction, pushing the boundaries of high-throughput materials characterization and paving the way for data-driven materials design. |
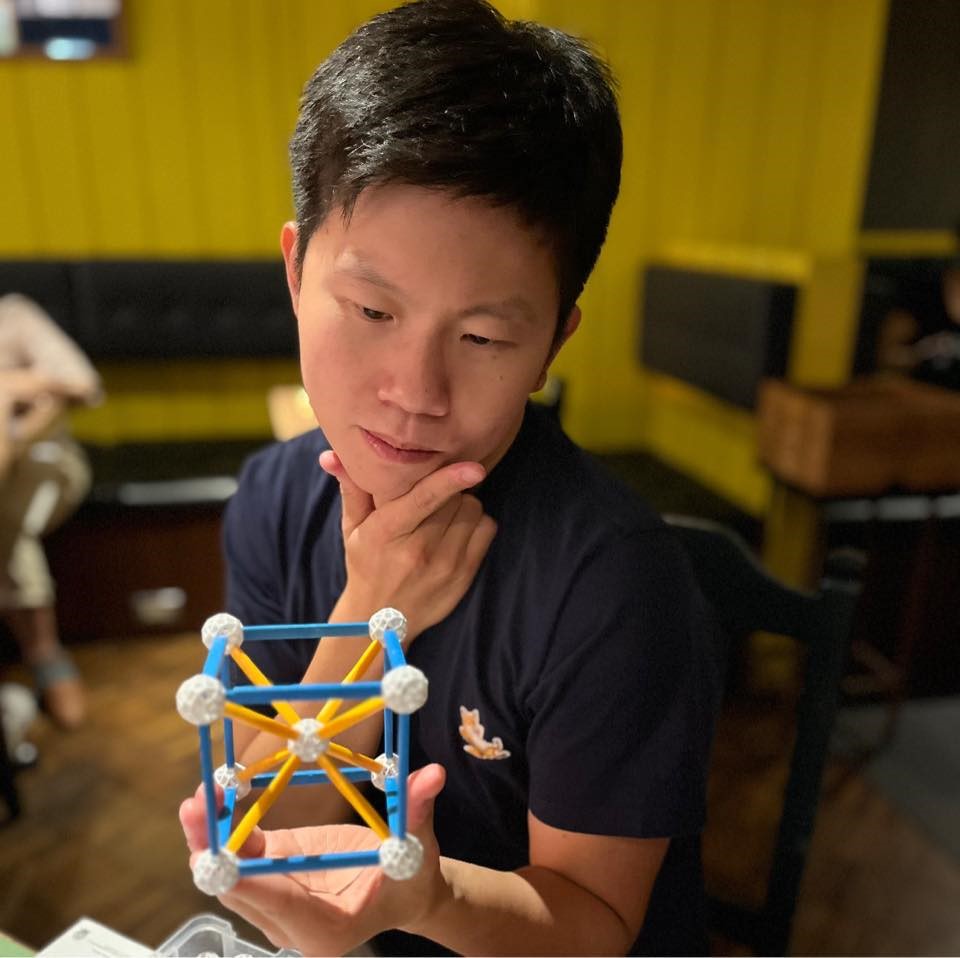 |
Bo-Shiuan Li (Bo) is currently an assistant professor at Departments of Mechanical & Materials Engineering at National Sun Yat-sen University, Taiwan. He led the Extreme Nanomechanics Group (X-MECH) focusing on better understanding deformation mechanics at the microstructural level. Techniques often used are small-scale mechanical tests and SEM-based deformation mapping. The improved knowledge will be used to design stronger materials capable of serving in more extreme environments. Bo obtained his DPhil in Materials from the University of Oxford in 2018, then stayed as a postdoc till 2020. He briefly joined TSMC as a RD engineer before returning to academia in 2022. |
Small-Scale Mechanical Testing of Semiconductor Materials
Bo-Shiuan Li
Vertical integration and compound semiconductor materials are emerging research areas in Taiwan’s semiconductor industry. Both require good understanding of its mechanical strength at the device length scale to prevent failure during service. In this talk, the role of small-scale mechanical testing in these areas will be discussed. Case studies on the small-scale mechanical behavior of direct bonded interfaces and 4H-SiC and its relevance to processing optimization will be demonstrated. Lastly, aspects on future developments of small-scale mechanical testing for semiconductor research will be point out. |
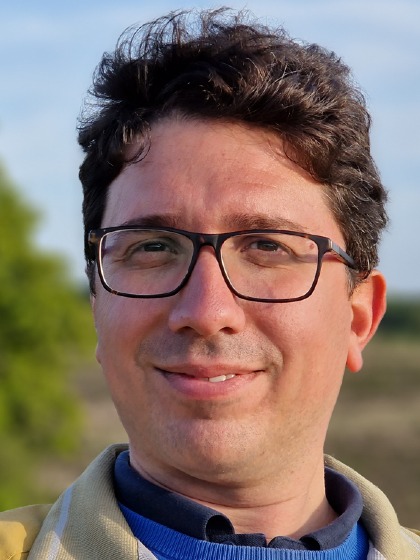 |
Francesco Maresca is currently Associate Professor in Engineering Mechanics and Materials Science, and Chair of the Mechanics of Materials research unit at the Engineering and Technology Institute (ENTEG) at the University of Groningen (Netherlands). He received his Ph.D. "cum laude" in Mechanical Engineering (Mechanics of Materials) at the Eindhoven University of Technology (TU/e) in 2015, working on a thesis about plasticity of martensite in low-alloyed steels. His thesis received multiple awards in the Netherlands, as well as abroad as the best PhD thesis in Europe in the field of metallurgy and materials science of steels (granted by Stahlinstitut VDEh Düsseldorf). After a postdoctoral research period (2015-2019) at EPFL, Switzerland, where he started his research on High Entropy Alloys together with his advisor Prof. Bill Curtin, he was appointed as Assistant Professor at the University of Groningen. His group's current focus is on multiscale modelling, including atomistics (Molecular Dynamics) and micromechanics (Crystal Plasticity), of dislocation plasticity, phase transitions and fracture in Advanced Steels and alloys including High Entropy Alloys. Applications include Wear of coatings, Hydrogen Embrittlement in steels, Liquid Metal Embrittlement and Functional Fatigue in Shape Memory Alloys. |
Multi-scale modelling of fracture from atomistics to micromechanics
Francesco Maresca
Fracture is a multiscale process that originates from atomic scale debonding, propagates across microstructural features and results into macroscopic failure at the engineering scale. Predicting the nano- and micro-scale mechanisms that control this phenomenon is crucial to addressing technological problems such as hydrogen embrittlement, liquid metal embrittlement and other environmental fracture phenomena. Here, by extending a 2D discrete dislocation dynamics framework, we first show the importance of crack-tip dislocation emission on enhancing fracture toughness in body-centered-cubic (BCC) metals. Next, we focus on the accurate prediction of the competition between emission and crack propagation by atomistic simulations. Modelling crack propagation is beyond reach of quantum-mechanical simulations (e.g. density functional theory, DFT). To overcome this bottleneck while retaining accuracy, we train and benchmark an array of state-of-the-art machine learning potentials (ML-IAPs) for ferromagnetic BCC iron, including the recent Atomic Cluster Expansion potentials. We use uncertainty quantification to assess the DFT-accuracy of the predicted dislocation structures and glide mechanisms, as well as active learning to predict the crack propagation mechanism. The ML-IAP is extended to model embrittlement e.g. due to hydrogen. |
|